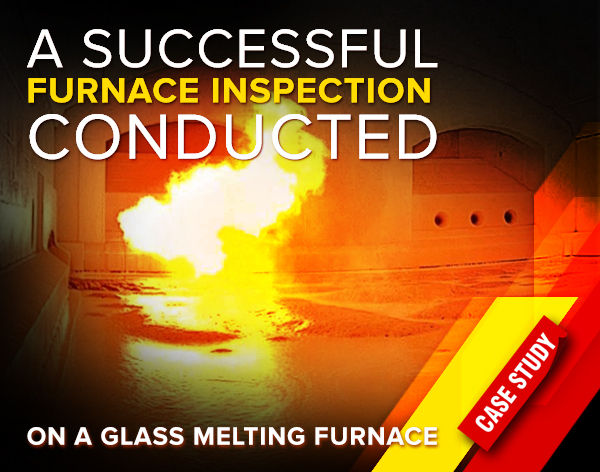
This case study presents the findings of a comprehensive furnace inspection conducted on a glass melting furnace. The inspection utilized an endoscopy technique with two camera angles (0 degrees and 90 degrees) to ensure complete coverage of the furnace. Access was granted to four peepholes within the furnace and an additional two peepholes in the regenerator. This approach allowed for a detailed examination of the furnace's condition and identified several significant concerns.
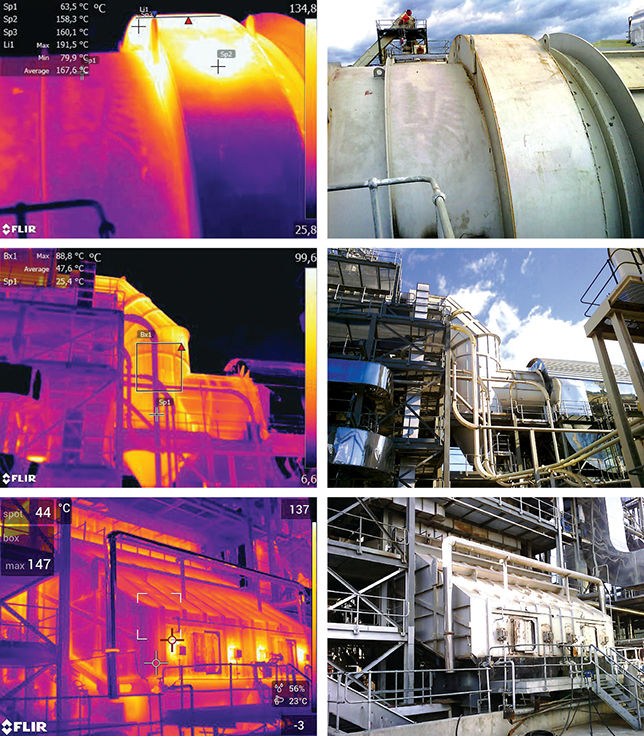
KEY FINDINGS:
REGENERATOR ISSUES:
The inspection revealed that approximately 80% of the checkers in the regenerator were blocked.
This obstruction severely impacted the efficiency of the regenerator and could potentially
impede the furnace's overall performance.
FLUX LINE WEAR:
Significant wear was observed along the flux line, suggesting a potential compromise in the integrity
of the refractory material. This wear could result in increased heat loss, reduced production efficiency,
and compromised safety.
MELTING GROWN BRICKS:
The inspection identified that the grown bricks in the furnace were melting, indicating excessive heat exposure. This condition may lead to the structural instability of the furnace and could result in catastrophic failure if left unaddressed.
DOGHOUSE ARCHES:
The doghouse arches were found to be in poor condition. This deterioration could cause uneven heat distribution, affecting the quality of the glass production and potentially leading to damage within the furnace structure.
CONCERNING HOTFACE BRICKS:
Several hotface bricks on the side walls were a cause for concern.
Their compromised condition indicated potential refractory failure, which could lead to heat leaks,
reduced energy efficiency, and increased operational costs.

THE INFORMATION UNCOVERED DURING THE FURNACE INSPECTION
IS CRITICAL TO THE CLIENT FOR THE FOLLOWING REASONS:
OPERATIONAL EFFICIENCY:
Resolving the blocked regenerator checkers improves furnace efficiency and production output.
COST SAVINGS:
Addressing issues minimizes energy waste, reduces operational expenses,and prevents
expensive emergency repairs.
PRODUCT QUALITY:
Fixing problems ensures consistent heat distribution, leading to better-quality glass production.
SAFETY AND RISK MITIGATION:
Repairing compromised components enhances safety and reduces the risk of accidents.
EQUIPMENT LONGEVITY:
Taking prompt action and conducting regular maintenance extends the furnace's lifespan,
avoiding premature replacements and saving on capital investments.

In summary, the critical information enables the client to optimize efficiency, reduce costs, maintain product quality, ensure safety, and prolong the furnace's lifespan for long-term business sustainability and a competitive edge.

ABOUT OUR COMPANY, HISTORY, AND PARTNERS
Dickinson Group of Companies (DGC) was founded in 1910. For comprehensive information about Our Company – History, Vision & Values, Strategy, Global Alliances, Africa Footprint, Our Commitment to Safety, Anti-Corruption Policy, References, and Industrial Solutions, please visit our websites.
