We recently received an inquiry from one of the biggest cement companies in the southern hemisphere to install refractory anchors and cast the nose ring at the entrance of the kiln.
The previous method resulted in increased downtime and maintenance due to the short-lasting liners. In light of this, we recommended a precast solution and installed the anchors and blocks before welding them onto the liners.

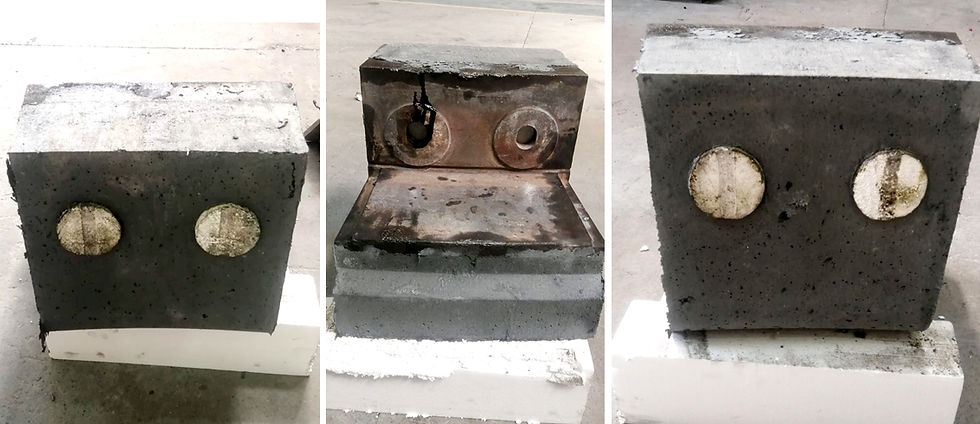
The refractory material was cast together with its binding liquid for better bonding. Our solution minimised downtime saving the client both time and money. The customer was extremely happy with the precast nose rings, which have since been in place for over 3 years.
As always we at DGC take pride in providing innovative solutions to our clients to enhance their productivity and efficiency.
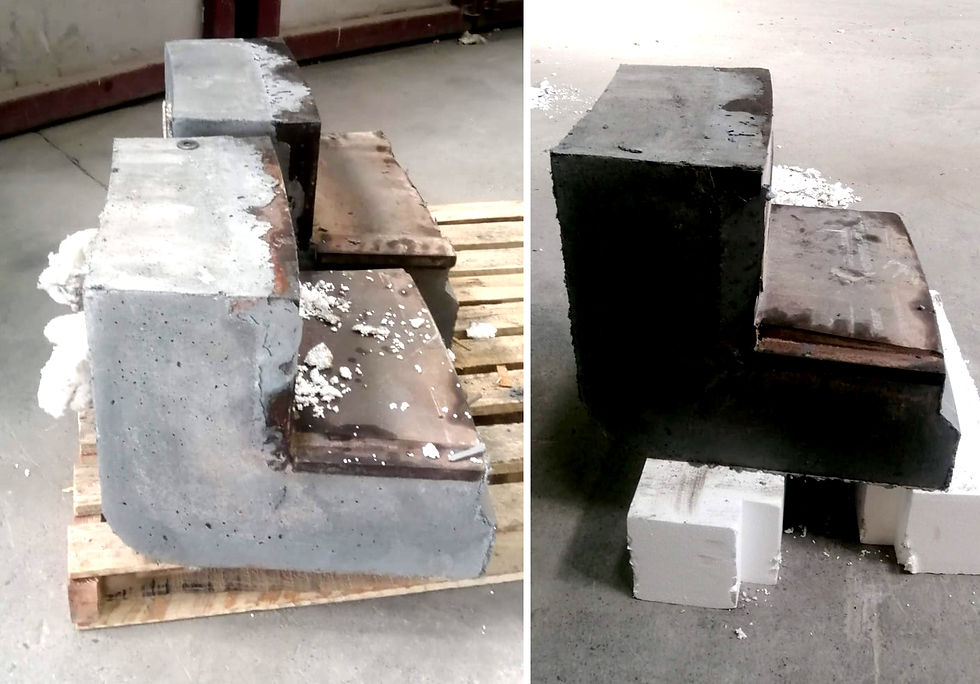
BENEFITS:
Consistent and controlled manufacturing process.
Unique purpose-developed materials and shapes for each application.
Work done off-site resulting in minimum interface with production.
Areas of higher wear can be engineered with optimal refractory materials.
Easier slag or dross removal due to lower porosity.
Less downtime due to quicker installation and heat-up times are minimized.
Shapes from 1 kg to 9 metric tons, resulting in fewer joints and faster installation
APPLICATIONS:
Anchors
Bitumen paint and refractory anchors caps
Welding
Mould manufacturing
The casting of the refractory material
Drying of the refractory material to the desired temperature supplied by the material manufacturer (Datasheet)
HOW TO GET IN TOUCH WITH US
Ask a DGC consultant to find out more about the Precast Refractory Shapes that we offer
sales@dgc-africa.com or sales@dgrpint.com

ABOUT OUR COMPANY, HISTORY, AND PARTNERS
Dickinson Group of Companies (DGC) was founded in 1910. For comprehensive information about Our Company – History, Vision & Values, Strategy, Global Alliances, Africa Footprint, Our Commitment to Safety, Anti-Corruption Policy, References, and Industrial Solutions, please visit our websites.
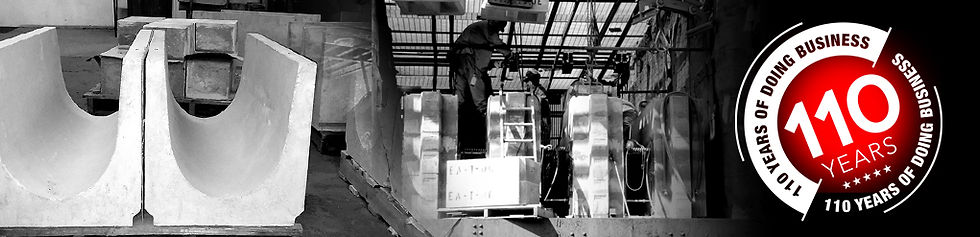