PUBLISHED IN CREAMER MEDIA'S MINING WEEKLY 28TH MAY 2021
There has been a significant increase in project activity for furnace services company Dickinson Group of Companies (DGC) since the start of this year.
DGC commercial manager Louwrens Minnie tells Mining Weekly that the impact of the Covid-19 pandemic caused a slump in activity last year, but that the business is doing “extremely well” now, with the company executing two major furnace rebuilds in the platinum sector.
“Some sectors, such as ferrochrome, are still sluggish, but overall, smelting plants are ramping up.” Minnie expects this uptick in activity to continue for at least the next 18 months, with numerous furnaces undergoing repair and maintenance work, in addition to major projects that involve complete rebuilds. There are also negotiations under way for a couple of brand new furnaces.
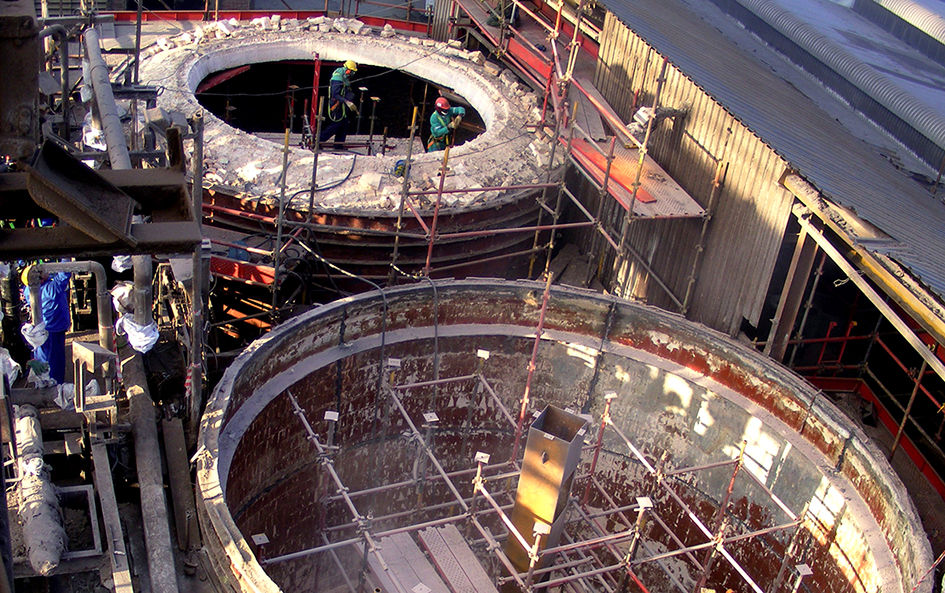
While the bulk of the work is in South Africa, the company is currently engaged in a few projects in Zambia and one in Saudi Arabia, with enquiries also trickling in from the Philippines.
Minnie notes that Covid-19 has impacted on the number and nature of long-term furnace maintenance contracts; traditionally, DGC would be on site almost daily to monitor and conduct ongoing repairs and maintenance.
“We have seen clients preferring to conduct more maintenance work over shorter periods to reduce the number of personnel on site at a time to reduce the risk of infection,” he says.
BRINGING THE A-GAME
Minnie believes that one of the main reasons why DGC has benefited from improved market conditions is that the company has earned the confidence of clients, owing to its wealth of experience in furnace services.
DGC entered the furnace business in 1928, when it was involved in the construction of one of South Africa’s first blast furnaces for then steel company Iscor Pretoria.
Since then, the company has been extensively involved in numerous greenfield and brownfield projects on industrial furnaces in the metals smelting, mineral process, power generation and petrochemical refining industries in sub-Saharan Africa, as well as in the Middle East, Scandinavia, Latin America, Russia and Commonwealth of Independent States countries.
DGC’s furnace services also include furnace demolition, mechanical installations, as well as refractory installation, and designing and manufacturing refractory shapes.
The company has also introduced furnace hotwork services to its service offering, which involve on-site heat treatment using mobile gas- or diesel-fired equipment. The furnace hotwork services offering also includes furnace cooldown, furnace expansion control, regenerator cleaning, insulation coating of regenerators, furnace hot repairs, temperature monitoring, post-weld heat treatment, as well as internal firings or temporary furnaces using diesel or gas burners.
The company has a large number of high-velocity burner sets that can be used for numerous furnace refractory drying-out and heat-up projects simultaneously.
DGC technicians are trained in-house according to the original-equipment manufacturer manuals to operate all the equipment optimally and safely.
“Our technicians are graded yearly to ensure that they are well qualified to undertake our furnace hotwork services in accordance with our safety and quality standards,” says Minnie.
DEMOLITIONS
Minnie says furnace demolitions performed by DGC now involve mechanised machinery, which is a direct benefit to clients because it makes the demolition safer, more efficient and more cost effective.
The demolitions can be achieved with significantly less personnel on site when compared with labour-intensive conventional methods.
Using mechanised machinery also allows for demolition at different scales – from confined spaces as small as 1 m3 using the remote controlled Brokk 5.0 robot, which weighs less than 500 kg, to much larger spaces using the Brokk 800, which weighs more than 11 t and is equipped with a 360º rotating arm that has a 10 m reach.
“These remote-controlled machines are highly beneficial in hot environments where a furnace is still running or has not yet fully cooled. It enables the operator to remain at a distance, thereby ensuring their safety,” Minnie explains.
DGC also uses high-powered crawler excavators and hydraulic breakers for furnace demolitions, in addition to mechanical dismantling and rigging, thermal oxygen lancing, liquid nitrogen cooling, controlled hot blasting and wire cutting on electrodes.
“The most dangerous part of doing furnace rebuilds is the demolition that first has to take place. This is why is it essential that we prioritise safety through investing in high-end equipment,” Minnie concludes.
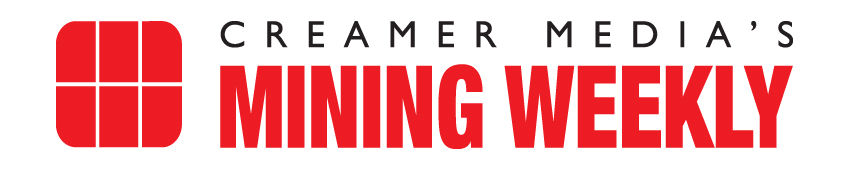
https://www.miningweekly.com/article/furnace-sector-heating-up-after-covid-19-2021-05-28