PUBLISHED IN CREAMER MEDIA'S MINING WEEKLY 28TH MAY 2021
Furnace services company Dickinson Group of Companies’ (DGC’s) new service offerings help to ensure more cost-effective furnace maintenance and repair. DGC added endoscopic furnace inspection services to its service offering, which is ideal for smaller scale maintenance and repair work, just prior to the pandemic outbreak.

DGC commercial manager Louwrens Minnie explains that endoscopic inspection at working temperature allows for the real-time, remote visualisation of the interior of a furnace during normal operations, consequently allowing for the assessment of the state of the refractories inside the unit.
“With this technology, one can see damage to the refractories, buildup on the sidewalls, the state of the bed of material within the furnace and the movement of the material, as well as where extensive wear is taking place on the refractory lining,” he tells Mining Weekly.
The robust, purpose-designed endoscopy devices can operate in the extremely harsh conditions inside furnaces. Probes are designed to have small diameters, thereby only requiring small openings – as small as 50 mm. Moreover, suitable endoscope lengths and various vision angles allow for enhanced flexibility during inspection.
To offer these services to clients, DGC has allied itself with Belgian industrial services company ADI Industrial Services, which designs and manufactures its own endoscopic devices, in line with the specified technical requirements of clients. Minnie notes that endoscopy can also be particularly helpful during so-called hot repairs such as for ceramic welding operations.

MINIMISING DOWNTIME
Since furnace endoscopy inspections are conducted at operating temperatures, there is no need to stop production operations and incur prolonged cooling times that conventional methods of inspection require.
He explains that furnace endoscopy is a proactive measure that allows for the timeous identification of several issues linked to the state of the furnace.
“It really is a useful tool for conducting preview inspections of units before implementing maintenance shutdowns, enabling more accurate costing and decreased downtime.”
During inspection, the specially designed water- or air-cooled camera is inserted through pre-existing inspection openings on strategically selected parts of the furnace system.
The camera is then manually manipulated to view angles of up to 360º within the unit. Images are captured and labelled according to the opening location and visualisation angle.
After inspection, images are taken for further processing, analysis and interpretation. Theoretically, the highly robust furnace endoscopy devices can be used to inspect units at any temperature.
Minnie explains that units operating at higher temperatures tend to provide clearer images, as the internal high-temperature glow provides improved lighting.
Typically, endoscopic inspections reveal varying extents of refractory lining wear. Depending on the extent of wear, accurate recommendations for repairs can then be made, he notes.
Such inspections also reveal open joints in brickwork, which could let heat leak through to inner refractory linings, which are often less tolerant to furnace working temperatures. The caulking of the open joints, as well as brick replacements, may be proposed to remedy this.
Minnie says the inspection can reveal burner flame issues, which could be an indication of issues with the air inlets, burner or fuel systems.
Further, wear on the burner block, mechanical damage on the burners, system blockages from material build-up and the assurance of the integrity of non damaged areas can be established through endoscopic inspection.
DGC also offers infrared thermography inspections, which involves the real-time visualisation of the thermal status of furnace equipment from the outside, without any need for contact.
The priority of the inspection is to detect hot spots and determine temperature measurements.
Once the information from the infrared thermography is processed, it is integrated into users’ preventive maintenance programmes to create a compilation of comprehensive records of refractory lining wear. The adoption of infrared thermography enables operators to constantly monitor the metallic shell status, identify and localise damaged areas internally and externally, and estimate the remaining refractory lining thickness, he concludes.
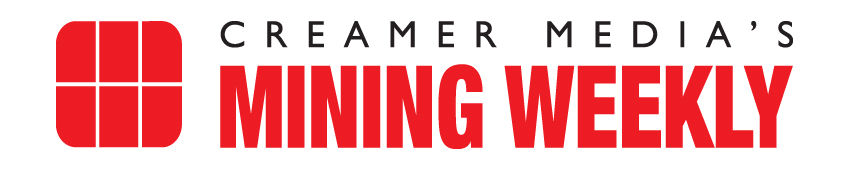