MAXIMIZING ROI: STRATEGIC REFRACTORY CHOICES FOR EFFICIENT AND DURABLE FURNACE OPERATIONS
- DGC AFRICA
- May 27, 2024
- 3 min read
In the competitive sphere of industrial furnace operations, where longevity and efficiency drive profitability, the strategic selection of refractory materials becomes crucial. These materials are foundational to operational success and pivotal in extending the intervals between costly furnace rebuilds. This week, we explore the impact of choosing cost-effective refractory solutions that enhance the lifecycle of furnace assets, optimizing capital expenditures in heavy industries, and offering a sustainable approach to furnace management.

THE CRUCIAL ROLE OF REFRACTORY MATERIALS IN FURNACE OPERATIONS
Refractory materials are engineered to confront extreme operational challenges, including intense heat, chemical corrosion, and constant mechanical stress. They are indispensable for:
THERMAL MANAGEMENT
Maintaining high temperatures efficiently within the furnace is crucial for energy conservation and process efficiency.
STRUCTURAL PROTECTION
Safeguarding the furnace’s integral structure from the ravages of heat and corrosive chemicals, thus preventing premature wear and failure.
OPERATIONAL LONGEVITY
Extending the operational lifespan of furnaces by providing resistance to mechanical and thermal shocks, which are common in high-stress environments.
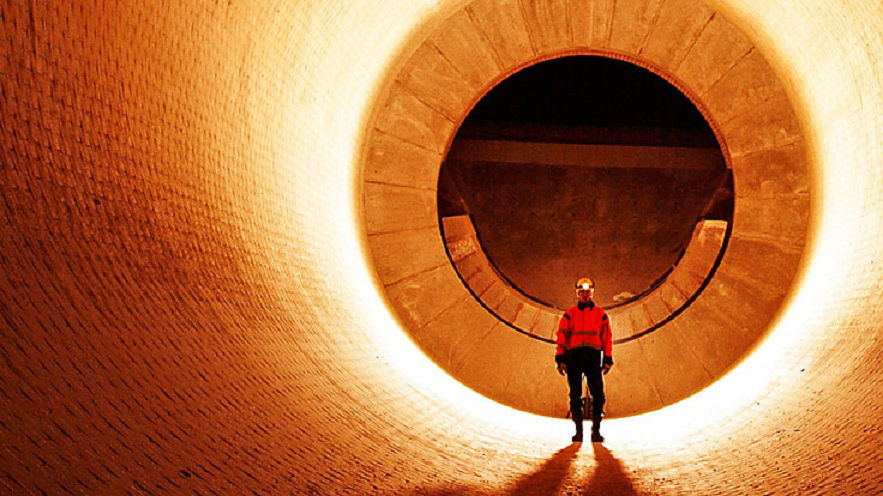
CHOOSING THE RIGHT REFRACTORY MATERIALS
The effectiveness of a refractory material is significantly determined by its composition and the specific operational demands it needs to meet:
FIRECLAY AND HIGH ALUMINA REFRACTORIES
These are cost-effective options known for their decent thermal resistance, making them suitable for applications involving moderate temperatures.
SILICA AND MAGNESITE REFRACTORIES
Ideal for high-temperature and corrosive settings, these materials offer superior durability and resistance to chemical reactions.
CARBON AND ZIRCONIA REFRACTORIES
These refractories are best suited for the most extreme conditions and provide unmatched thermal conductivity and resistance, essential in reducing atmospheres in processes like steel smelting.
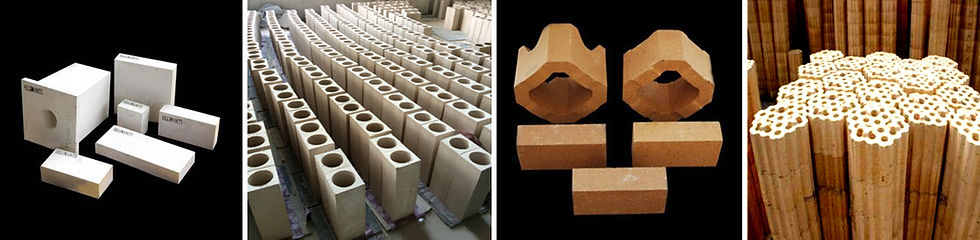
ACHIEVING COST-EFFECTIVENESS WITH REFRACTORY MATERIALS
Efficiency in refractory materials stems from several factors that influence both the initial investment and long-term operational costs:
MATERIAL SELECTION
Choosing the right materials, such as fireclay for its cost-effectiveness and durability, is tailored to specific furnace conditions.
MANUFACTURING PROCESS
Streamlining production processes to reduce manufacturing costs while maintaining quality.
DURABILITY AND MAINTENANCE NEEDS
Opting for materials that withstand harsh conditions for longer periods, thereby reducing the frequency and cost of replacements.
ENERGY EFFICIENCY
Utilizing insulating refractories that significantly reduce energy consumption by minimizing heat loss.
SUPPLY CHAIN OPTIMIZATION
Ensuring the supply chain is robust and efficient, reducing logistical costs, and improving delivery timelines.
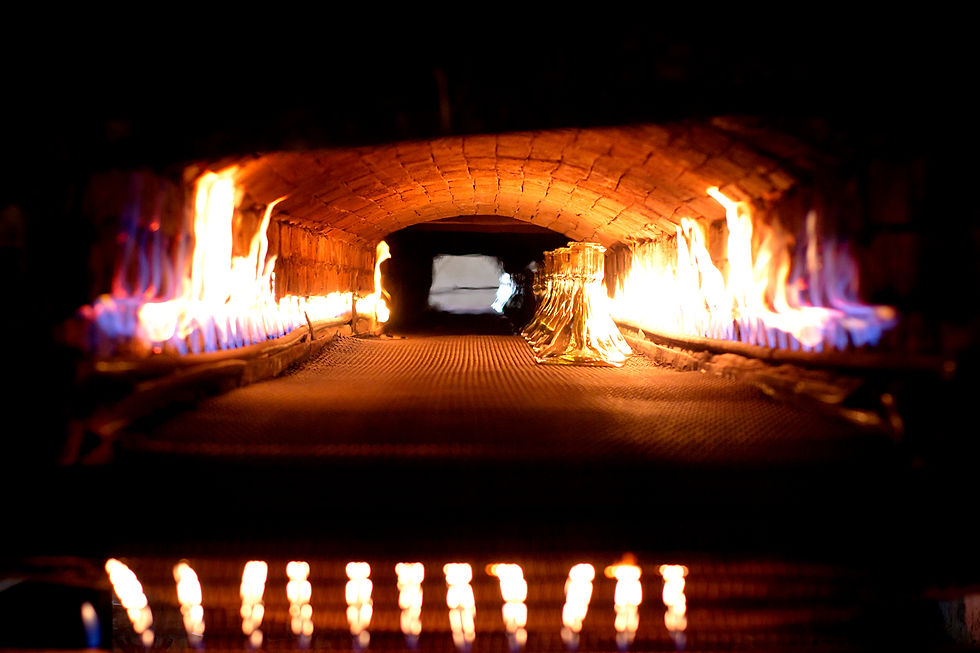
STRATEGIC APPROACHES TO BALANCING COST AND PERFORMANCE
To maximize the return on investment, industries must adopt a holistic approach that considers the total cost of ownership. This includes not only the initial expenditure on refractory materials but also ongoing costs associated with installation, maintenance, and operation. Employing cutting-edge material technologies, such as nano-enhanced refractories, and incorporating smart systems that facilitate real-time monitoring can drastically enhance the performance and longevity of furnace operations. Proper design and professional installation are imperative to ensure refractories perform optimally under specific operational conditions, thereby securing a worthwhile investment.
INNOVATIONS SHAPING THE FUTURE OF REFRACTORIES
The refractory material industry is witnessing significant technological advancements that promise to transform furnace operations. Innovations such as nanotechnology are enhancing the density and durability of refractories, thereby extending their service life. Eco-friendly materials and processes are reducing the environmental impact of refractory production. Additionally, the integration of smart technologies like IoT sensors within refractory systems enables predictive maintenance, which minimizes downtime and extends the operational life of furnaces, thus optimizing maintenance schedules and costs.
The strategic selection of cost-effective refractory materials significantly enhances furnace efficiency and safety, reducing the frequency and cost of rebuilds. At DGC AFRICA, we are dedicated to pioneering refractory solutions that align with both cost-efficiency and superior performance, ensuring our clients receive the best return on their investments in industrial furnace operations.
Discover how DGC AFRICA’s innovative and cost-effective refractory solutions can transform your furnace operations.
Visit our Insights Section or contact our expert team today
to learn more about our tailored refractory solutions that meet your specific needs.

ABOUT OUR COMPANY, HISTORY, AND PARTNERS
Dickinson Group of Companies (DGC) was founded in 1910. For comprehensive information about Our Company – History, Vision & Values, Strategy, Global Alliances, Africa Footprint, Commitment to Safety, Anti-Corruption Policy, References, and Industrial Solutions, please visit our website.

Kommentare