TYPES OF REFRACTORY ANCHORS SYSTEMS
- DGC AFRICA
- Oct 21, 2021
- 1 min read
Metal anchoring systems are widely utilized to support refractory materials in various vessels in high temperature industries.
In fact, the design of high performance, reliable furnaces and pyrometallurgical vessels are incomplete without the inclusion of monolithic refractory linings and anchoring. The importance of refractory anchor systems can never be overstated as they can have an impact on the actual service life of refractory linings.
Dickinson Group of Companies uses wire coils that adhere to strict internal material specifications and has undergone the annealing process. Anchors are produced by means of free bending on the CNC-3D bending machine; ensuring the anchors’ ability to meet the required quality standards. With state-of-the-art manufacturing facilities, in-house design capabilities and rapid response services; the resulting unique range of anchor systems increase performance, speeds up installations and saves money for the clients.
The range of refractory anchor systems is generally classified into the following categories
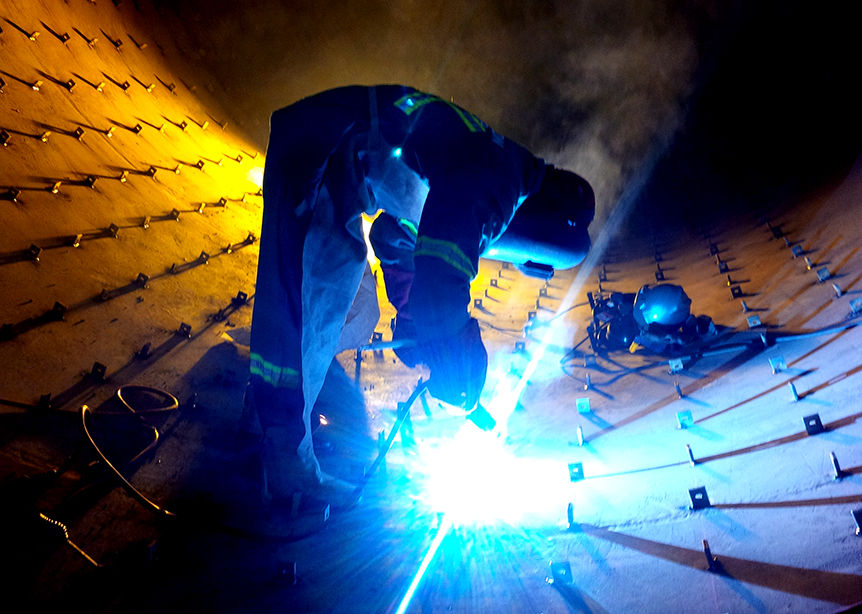
MONOLITHIC REFRACTORY ANCHORS
Standard and custom-made refractory anchors for monolithic linings.
Single and Multi-Layer linings – Y series, V series and Bullhorn.
Steel Alloy grades: 304, 316, 310 and 253ma.
Various thicknesses including 5.5, 6, 8, 10 and 12 mm.
REFRACTORY BRICK ANCHORS
Standard and custom-made refractory anchors for brick linings.
Staples, Scissor Clips, Claws, Tie Back Anchors, Support Brackets.
CERAMIC FIBRE ANCHORS
Systems suitable for anchoring ceramic fibre linings over a range of operating temperatures.
Press on Clip Systems, Threaded, Fibre-lock Pins, Lock Washers and Spring Clip Washers.
REFRACTORY ARMOUR SYSTEMS
For process plants, in areas which are subject to the passage of erosive gas streams, particularly at high temperature.
REINFORCING FIBRES
The use of stainless steel alloy fibres substantially improves refractory durability and performance.
Comments